Accuracy Issues: Welding Inspection Service for Flawless Welds
Accuracy Issues: Welding Inspection Service for Flawless Welds
Blog Article
Revealing the Diverse Array of Welding Providers and Their Benefits
As markets proceed to require and evolve precision in their production processes, the relevance of welding services has actually come to be significantly noticable. From the versatility of arc welding to the effectiveness of MIG welding, and the complex work accomplished via TIG welding to the accuracy of laser welding, the range of welding techniques readily available is substantial. Each technique brings its own collection of advantages and applications, satisfying a wide array of requirements across numerous fields. Recognizing these varied welding solutions and their benefits can give valuable understandings into maximizing fabrication procedures and accomplishing premium results.
Kinds Of Welding Services
Among the various types of welding solutions available, each offers unique benefits and applications in different markets. One usual kind is MIG welding, likewise called Gas Steel Arc Welding (GMAW), which makes use of a cable electrode to join metals with each other. MIG welding is valued for its speed and adaptability, making it appropriate for a vast array of materials consisting of aluminum, steel, and stainless steel. One more commonly used approach is TIG welding, or Gas Tungsten Arc Welding (GTAW), which utilizes a non-consumable tungsten electrode to produce a specific and tidy weld. TIG welding is favored for its ability to produce high-grade welds in thin products, making it ideal for sectors such as aerospace and vehicle.
Furthermore, there is Stick welding, or Protected Metal Arc Welding (SMAW), which is understood for its simpleness and efficiency, specifically in windy or outdoor conditions. This method is typically made use of in building and construction and pipeline welding. Lastly, there is Flux-Cored Arc Welding (FCAW), which is a versatile procedure ideal for thick products and can be made use of in both automated and semi-automatic applications. Each sort of welding service has its strengths and is picked based upon aspects such as product kind, thickness, and the certain needs of the task at hand.
Advantages of Arc Welding
Arc welding offers a wide variety of benefits that accommodate various commercial requirements and needs. One of the key benefits of arc welding is its versatility. Welding Inspection Service. This welding approach can be utilized on a variety of steels and alloys, making it a prominent selection for markets collaborating with diverse products. Additionally, arc welding is understood for its high welding speeds, which can significantly boost efficiency in manufacturing processes. The procedure is additionally relatively easy to automate, lowering labor costs and improving general effectiveness.
One more key advantage of arc welding is its capability to produce strong and sturdy welds. The warm produced during the process aids to create a metallurgical bond in between the base metals, leading to welds that have the ability to hold up against high degrees of stress and stress. Arc welding also creates precise and clean welds, reducing the demand for extra finishing job. On the whole, the benefits of arc welding make it an important tool for numerous industries wanting to attain top quality welds effectively.
Advantages of MIG Welding
With a focus on effectiveness and durability in welding processes, MIG welding offers a distinctive collection of benefits that match the convenience and stamina found in arc welding. MIG welding, or Gas Steel Arc Welding (GMAW), is known for its speed and simplicity of use. The process involves feeding a cable electrode with a welding weapon, Check Out Your URL which is then melted and used to sign up with the base materials together. Among the key benefits of MIG welding is its high welding rates, making it a favored option for jobs that need quick turn-around times.
Additionally, MIG welding creates clean welds with very little splatter, lowering the demand for substantial cleanup after the welding process. The flexibility of MIG welding permits welding a broad variety of products, consisting of aluminum, stainless steel, and moderate steel. This adaptability makes MIG welding suitable for various markets, from auto to building.
Moreover, MIG welding is recognized for its high deposition rates, suggesting even more product can be transferred in a shorter quantity of time compared to various other welding processes. This leads to increased performance and cost-effectiveness for jobs that call for large quantities of welds. In general, the benefits of MIG welding make it an important technique for accomplishing efficient and sturdy welds throughout various applications.
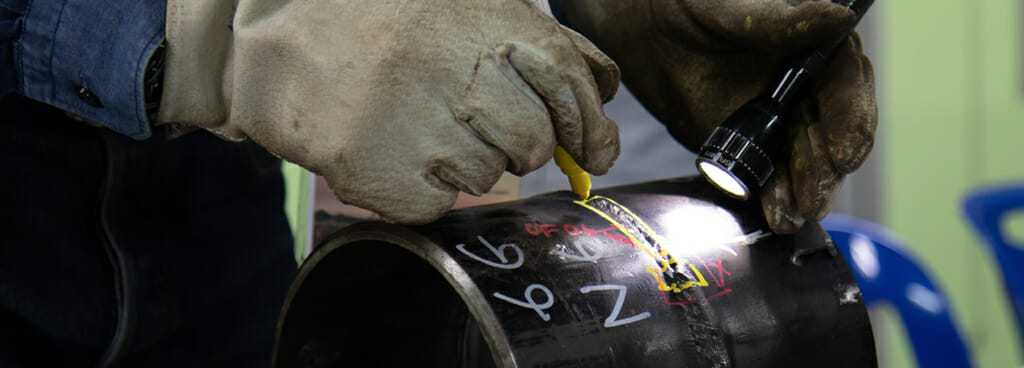
Discovering TIG Welding Advantages
TIG welding, likewise called Gas Tungsten Arc Welding (GTAW), supplies a distinct collection of advantages that satisfy accuracy and control in welding applications. One of the main benefits of TIG welding is its ability to produce top notch, tidy welds without the demand for filler material. This makes it suitable for welding slim products where aesthetic appeals and precision are vital, such as in the aerospace and vehicle industries. Furthermore, TIG welding supplies excellent control over the warm input, resulting in marginal distortion of the workpiece.
Additionally, TIG welding can be used on a broad array of steels, consisting of stainless steel, copper, aluminum, and titanium, making it a flexible choice for various welding tasks. The procedure likewise enables for welding in different settings, providing adaptability in tough welding situations.
Benefits of Laser Welding

An additional advantage of laser welding is its flexibility in dealing with a wide variety of materials, including steels, plastics, and even dissimilar products. This adaptability makes laser welding appropriate for diverse markets such as automobile, aerospace, electronic devices, and medical devices. The non-contact nature of laser welding likewise minimizes contamination, making it a ecologically friendly and clean welding method.
In addition, laser welding allows complicated and intricate weld geometries that might be challenging to achieve with typical welding strategies. This ability opens new design possibilities and permits the production of lighter and more innovative elements - Welding Inspection Service. Overall, the benefits of laser welding make it a recommended choice for lots of manufacturing applications seeking high accuracy and efficiency
Final Thought

Arc welding offers strong and long lasting welds, while moved here MIG welding provides see this effectiveness and adaptability. TIG welding ensures tidy and specific welds, and laser welding gives high accuracy and rate.
From the versatility of arc welding to the effectiveness of MIG welding, and the complex job completed through TIG welding to the precision of laser welding, the array of welding methods offered is huge. One common kind is MIG welding, likewise known as Gas Metal Arc Welding (GMAW), which utilizes a cable electrode to sign up with metals with each other. Additionally, arc welding is known for its high welding speeds, which can substantially boost productivity in producing processes.With an emphasis on efficiency and durability in welding processes, MIG welding provides a distinctive collection of benefits that match the adaptability and strength discovered in arc welding.TIG welding, additionally understood as Gas Tungsten Arc Welding (GTAW), provides a distinctive collection of advantages that cater to precision and control in welding applications.
Report this page